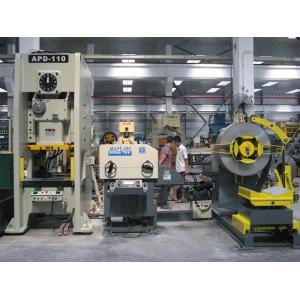
Add to Cart
NC servo feeder performance is stable _ Ruihui high-precision nc servo feeder _ you can rest assured
The NC servo feeder has stable performance and extremely low failure rate. It is only the best stamping equipment. In actual use, the occurrence of faults is still inevitable. The NC servo feeder is no exception. The most common fault is the unstable transmission distance. In the event of such a failure, timely targeted treatment is required to prevent the loss of stamping production caused by inaccurate feeding.
The unstable transmission distance of the NC servo feeder is also called infeed, which will greatly affect the quality of the stamped product; the seven factors that affect the inaccurate feeding:
1. The setting speed of the NC servo feeder is too fast: the NC servo feeder is not capable of high-speed feeding due to the response time of the electronic control system. Generally, the maximum feeding speed of the pneumatic NC servo feeder is 60-120 times per minute ( The specific number varies depending on the material thickness and step size.) The maximum feeding speed of the mechanical NC servo feeder is 150-200 times per minute. If the actual punching speed is higher than this speed, the NC servo feeder will not keep up. And caused the wrong material.
2. The external air supply pressure is too large or not enough. The NC servo feeder needs a stable air supply to achieve fast and stable relaxation. The three-point combination pressure gauge needs to be adjusted to 4.5kg/cm2. Treatment method: Check whether the three-point combination pressure gauge is damaged and adjust the compressor pressure.
3. The feeding height of the NC servo feeder is incorrect. Punch often needs to be used with multiple sets of different molds. The height of different molds can also be different. At this time, the feed height of the feeder should be adjusted after changing the mold. If the adjustment is not correct, the feed will be skewed and uneven. Adjust the feed height of the feeder to keep it horizontal and vertical with the mold.
4. There is an error in the punching die itself or no material trimming. If there is a problem in the design and production of the punching die itself, the feeding distance will be unstable. At this time, the NC servo feeder can be used for feeding, but the manual manual feeding is used to test the product to confirm whether the problem is on the mold itself. Modification can be done.
5. There is stamping oil on the feeding roller of NC servo feeder. Stamping production In order to prevent the long-term friction between the material and the mold, the die life is damaged and the punching accuracy is not accurate. Usually, the material is stamped with oil before the material enters the mold. If the punching oil enters the feeding roller, the feeding slip will be inaccurate. At this time, the feed roller can be cleaned and wiped.
6. The feeding time of the NC servo feeder is set incorrectly. Different molds have different feeding time requirements for the feeder. If the feeding time is set too late, the feeding will be insufficient. At this time, the feeding signal cam angle of the punching machine needs to be re-adjusted.
7. The NC servo feeder's relaxation time is incorrect. If the relaxation time is not correct, the material feeding will not be in place or the material will retreat. At this time, the angle of the relaxation signal cam of the punching machine needs to be re-adjusted.
Specification:
Model | MAC2-400 | MAC2-500 | MAC2-600 | MAC2-800 | ||
Stock Width(mm) | 50-400 | 50-500 | 50-600 | 50-800 | ||
Stock Thickness(mm) | 0.3~3.2 | 0.3-3.2 | 0.3-3.2 | -3.2 | ||
Max.Coil Weight(kg) | 3000 | 3000 | 3000 | 5000 | 5000 | 7000 |
Max.Coil O.D.(mm) | 1200 | 1200 | 1200 | |||
Coil I.D.(mm) | 8 | 8 | 508 | 508 | ||
Feed Length(mm) | ~500* | ~500* | ~500* | ~500* | ||
Max. Line Speed(m/min) | 16-24 | 16-24 | 16-24 | 16-24 | ||
Work Roll Number(pieces) | upper 6 lower 5 | upper 6 lower 5 | upper 6 lower 5 | upper 6 lower 5 | ||
Feed Roll Number(set) | 1 | 1 | 1 | 1 | ||
Main Motor(kw) | AC2.9 | AC2.9 | AC4.4 | AC4.4 | ||
Mandrel Expansion | hydraulic | hydraulic | hydraulic | hydraulic | ||
Reel Motor(kw) | 1.5 | 1.5 | 1.5 | 2.2 | 2.2 | 3.7 |
Power(V) | 3 Phase 220V/380V/50HZ | |||||
Operating Air(Mpa) | 0.49 | 0.49 | 0.49 | 0.49 |
Straigtening performance:
tock Thicknees (mm) | Stock Width (mm) | |||
0.3 | 400 | 500 | 600 | 800 |
0.4 | ||||
0.6 | ||||
0.8 | ||||
1.0 | ||||
1.2 | ||||
1.4 | ||||
1.6 | 470 | 470 | ||
1.8 | 400 | 400 | ||
2.0 | 360 | 360 | ||
2.3 | 300 | 300 | 300 | 300 |
2.5 | 230 | 230 | 230 | 230 |
2.8 | 150 | 150 | 150 | 150 |
3.2 | 110 | 110 | 110 | 110 |
*1:(Pneumatic):Option in case of pneumatic mandrel expansion is provi