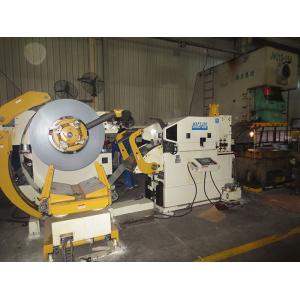
Add to Cart
The precise feeding step of the punch feeder is one of the significant advantages compared to manual feeding. After the feeder is installed in the press, it is usually necessary to test its feed step to verify that its performance is stable.
Attention should be paid during the test: the actual feeding position of the punching machine is not accurate, which may be the reason of the feeding machine, the reason of the mold, or other external reasons.
Therefore, it is necessary to use two methods of step test without installing the mold and step test after installing the mold to comprehensively determine.
1. No mold is installed, single press processing test, it is not suitable for feeding of high speed roller feeder.
Test method: adjust the feeding step, single-run the punch, feed once to mark the position after feeding, after a single operation for ten times, cut the strip, test the 10 mark feeding values, see the punch feeder step Whether the distance is accurate.
2. do not install the mold, multiple stamping processing test, it is suitable for the punch feeder equipment.
Test method: adjust the feeding step, mark the material once before the initial feeding, then mark the mark after using the continuous punching ten times, then return the material to the mark before the first feeding, and then restart Use the continuous feeding ten times and repeat the third marking.
3. After installing the mold, after multiple feedings, check whether the product meets the accuracy requirements.
Feeding step determination is usually used using 1 and 3 or 2 and 3 combinations. If 1, 2 is accurate and 3 is not accurate, the problem is on the mold.
If 1, 2, and 3 are inaccurate, the problem lies in the press feeder. It is necessary to check the air source, the feeding relaxation angle, etc. If the customer can't find the reason, you can call the Ruihui after-sales department at any time.
Specification:
Model | MAC2-400 | MAC2-500 | MAC2-600 | MAC2-800 | ||
Stock Width(mm) | 50-400 | 50-500 | 50-600 | 50-800 | ||
Stock Thickness(mm) | 0.3~3.2 | 0.3-3.2 | 0.3-3.2 | -3.2 | ||
Max.Coil Weight(kg) | 3000 | 3000 | 3000 | 5000 | 5000 | 7000 |
Max.Coil O.D.(mm) | 1200 | 1200 | 1200 | |||
Coil I.D.(mm) | 8 | 8 | 508 | 508 | ||
Feed Length(mm) | ~500* | ~500* | ~500* | ~500* | ||
Max. Line Speed(m/min) | 16-24 | 16-24 | 16-24 | 16-24 | ||
Work Roll Number(pieces) | upper 6 lower 5 | upper 6 lower 5 | upper 6 lower 5 | upper 6 lower 5 | ||
Feed Roll Number(set) | 1 | 1 | 1 | 1 | ||
Main Motor(kw) | AC2.9 | AC2.9 | AC4.4 | AC4.4 | ||
Mandrel Expansion | hydraulic | hydraulic | hydraulic | hydraulic | ||
Reel Motor(kw) | 1.5 | 1.5 | 1.5 | 2.2 | 2.2 | 3.7 |
Power(V) | 3 Phase 220V/380V/50HZ | |||||
Operating Air(Mpa) | 0.49 | 0.49 | 0.49 | 0.49 |
Straigtening performance:
tock Thicknees (mm) | Stock Width (mm) | |||
0.3 | 400 | 500 | 600 | 800 |
0.4 | ||||
0.6 | ||||
0.8 | ||||
1.0 | ||||
1.2 | ||||
1.4 | ||||
1.6 | 470 | 470 | ||
1.8 | 400 | 400 | ||
2.0 | 360 | 360 | ||
2.3 | 300 | 300 | 300 | 300 |
2.5 | 230 | 230 | 230 | 230 |
2.8 | 150 | 150 | 150 | 150 |
3.2 | 110 | 110 | 110 | 110 |
*1:(Pneumatic):Option in case of pneumatic mandrel expansion is provi