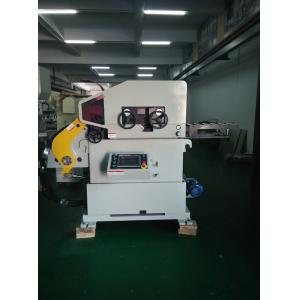
Add to Cart
Roller feeder automatic feeding, metal processing materials, punch automation
Discharging process: the material to be processed is placed on the support frame of the Ruihui roller feeder, and the material is manually introduced into the upper and lower feeding rollers by the lifting handle to be fed into the mold. The pallet ensures that the roller feeder feeds smoothly and the material does not deflect.
Roller feeder working process: the punch slider moves downward, driving the output shaft to rotate counterclockwise, and the adjustable pull rod moves downwards, so that the rocker arm moves downwards, and the gear is driven to rotate clockwise. Since the bearing is a one-way bearing, this When feeding the roller and not rotating.
The slider relaxes the bracket to press the Palin while doing the downward movement, so that the feeder relaxes the screw to drive the relaxation device to lift the shaft as the axis upwards, and its purpose is to relax the taut material.
Because the downward movement of the slider at this time is when the mold is closed, the mold has already pressed the material at this time, so the positive guide pin of the mold is inserted into the guide hole, and the material relaxation device functions.
The punch slider moves upward to drive the output shaft to rotate clockwise, and the adjustable pull rod moves upward to make the rocker arm move upwards, and the gear is driven to rotate counterclockwise, because the bearing is a one-way bearing.
So at this time it drives the upper and lower feed rollers to rotate relative to each other and feed the material into the mold. When the slider is moving upwards, the feeder relaxes the bracket and disengages from the Palin, so that the relaxation device returns to the original position, because the upward movement of the slider is when the mold is opened, and the material moves according to the set step.
Thus, with the reciprocating motion of the punch slider, the automatic feeding action of the roller feeder also reciprocates.
Products:
Specification:
Model | MAC2-400 | MAC2-500 | MAC2-600 | MAC2-800 | ||
Stock Width(mm) | 50-400 | 50-500 | 50-600 | 50-800 | ||
Stock Thickness(mm) | 0.3~3.2 | 0.3-3.2 | 0.3-3.2 | -3.2 | ||
Max.Coil Weight(kg) | 3000 | 3000 | 3000 | 5000 | 5000 | 7000 |
Max.Coil O.D.(mm) | 1200 | 1200 | 1200 | |||
Coil I.D.(mm) | 8 | 8 | 508 | 508 | ||
Feed Length(mm) | ~500* | ~500* | ~500* | ~500* | ||
Max. Line Speed(m/min) | 16-24 | 16-24 | 16-24 | 16-24 | ||
Work Roll Number(pieces) | upper 6 lower 5 | upper 6 lower 5 | upper 6 lower 5 | upper 6 lower 5 | ||
Feed Roll Number(set) | 1 | 1 | 1 | 1 | ||
Main Motor(kw) | AC2.9 | AC2.9 | AC4.4 | AC4.4 | ||
Mandrel Expansion | hydraulic | hydraulic | hydraulic | hydraulic | ||
Reel Motor(kw) | 1.5 | 1.5 | 1.5 | 2.2 | 2.2 | 3.7 |
Power(V) | 3 Phase 220V/380V/50HZ | |||||
Operating Air(Mpa) | 0.49 | 0.49 | 0.49 | 0.49 |
Straigtening performance:
tock Thicknees (mm) | Stock Width (mm) | |||
0.3 | 400 | 500 | 600 | 800 |
0.4 | ||||
0.6 | ||||
0.8 | ||||
1.0 | ||||
1.2 | ||||
1.4 | ||||
1.6 | 470 | 470 | ||
1.8 | 400 | 400 | ||
2.0 | 360 | 360 | ||
2.3 | 300 | 300 | 300 | 300 |
2.5 | 230 | 230 | 230 | 230 |
2.8 | 150 | 150 | 150 | 150 |
3.2 | 110 | 110 | 110 | 110 |
*1:(Pneumatic):Option in case of pneumatic mandrel expansion is provi